Smart Thinking
Heat Pump and Heat Recovery Systems For Industrial Applications – Decarbonising Heat Production To Achieve Net-Zero Targets

The UK’s ambitious Net Zero goal of 2050 means that businesses are under pressure to develop and implement decarbonisation strategies. Some sectors have already published their strategies and others are being urged to publish detailed...Read More
The technology that will shape the future of the Cold Chain

Increasing global temperatures and energy costs, along with a scarcity of resources are forcing changes in our approach to power consumption in the cold chain. There is a need to adapt in order to continue...Read More
Reviving aging infrastructure: Lineage Logistics’ successful plant optimisation for a sustainable future

It’s estimated that the cold chain accounts for approximately 2–4% of UK GHG emissions. Data obtained from the UK Cold Chain Federation for 425 facilities registered with their Climate Change Agreement (CCA) Scheme during 2018...Read More
Long Term Refrigerants – Ammonia vs. CO2: Find your optimal refrigerant and balance your business needs for competitiveness, compliance and cooling efficiency

As legislation evolves to meet global environmental goals, refrigeration system owners and operators will need to be aware of how these changes affect their existing cooling equipment and what needs to be considered when making...Read More
The new F-Gas Regulation phase down (draft proposal April 2022)

What does the proposed new F-gas Regulations revision mean for the users and operators of cooling equipment? We are almost at the halfway point of the planned F-gas phase-down and on 5th April 2022, the...Read More
Carbon Dioxide Hazard and Safety Requirement Assessment – a systematic approach to risk assessment and emergency planning.

Carbon Dioxide (R744) is an odourless gas and can cause harm when incidents occur resulting in its release. For owners and operators of carbon dioxide refrigerated systems it is essential to understand best practice, in...Read More
Will data and AI lead to a more efficient cold chain?

As the refrigeration industry attempts to chart the route to Net Zero, a new energy forecasting tool harnesses data from industrial refrigeration systems to help the cold storage operators better manage energy consumption and CO2...Read More
An introduction to river water ammonia heat pumps for district heating

In a world where climate change and global warming are increasingly pressing concerns, it’s incumbent on all businesses, municipal bodies and private citizens to curb their carbon footprint as much as possible. Globally, heat accounts...Read More
Mapping the path to net zero in the industrial refrigeration sector

In December 2018, celebrated naturalist Sir David Attenborough called climate change “our greatest threat in thousands of years”. The following year, the British government became the first major economy to enshrine net-zero emissions goals into...Read More
The use of SEC as a predictive metric for business performance in the TCS&D sector

The price of electricity in the UK today is roughly double what it was a decade ago. There is also greater volatility in the pricing market, making future expenditure more difficult to calculate. Given that...Read More
The Internet of Things and The Evolution of Refrigeration Plant Aftercare

Jeff Gurnett, Star Refrigeration Regional Manager –North, talks about the real benefits the Internet of Things bring to the efficient and safe provision of planned preventative maintenance of industrial refrigeration equipment through smart monitoring of...Read More
The Journey to Net Zero – Industrial Refrigeration

The COVID-19 pandemic has highlighted the importance of industrial refrigeration in our modern society, delivering vital cooling for sectors including food production, temperature controlled storage, data processing and vaccine production. The projected growth of the...Read More
Delivering first class industrial refrigeration maintenance to owners and operators of cooling equipment

For over 50 years, Star Refrigeration has focused on providing a high quality service to our customers, resulting in one of the best retention rates in the industry. Pat Draper, Star’s regional manager for the...Read More
The Star SEC Calculator App – the first step on the temperature controlled storage journey to Net Zero
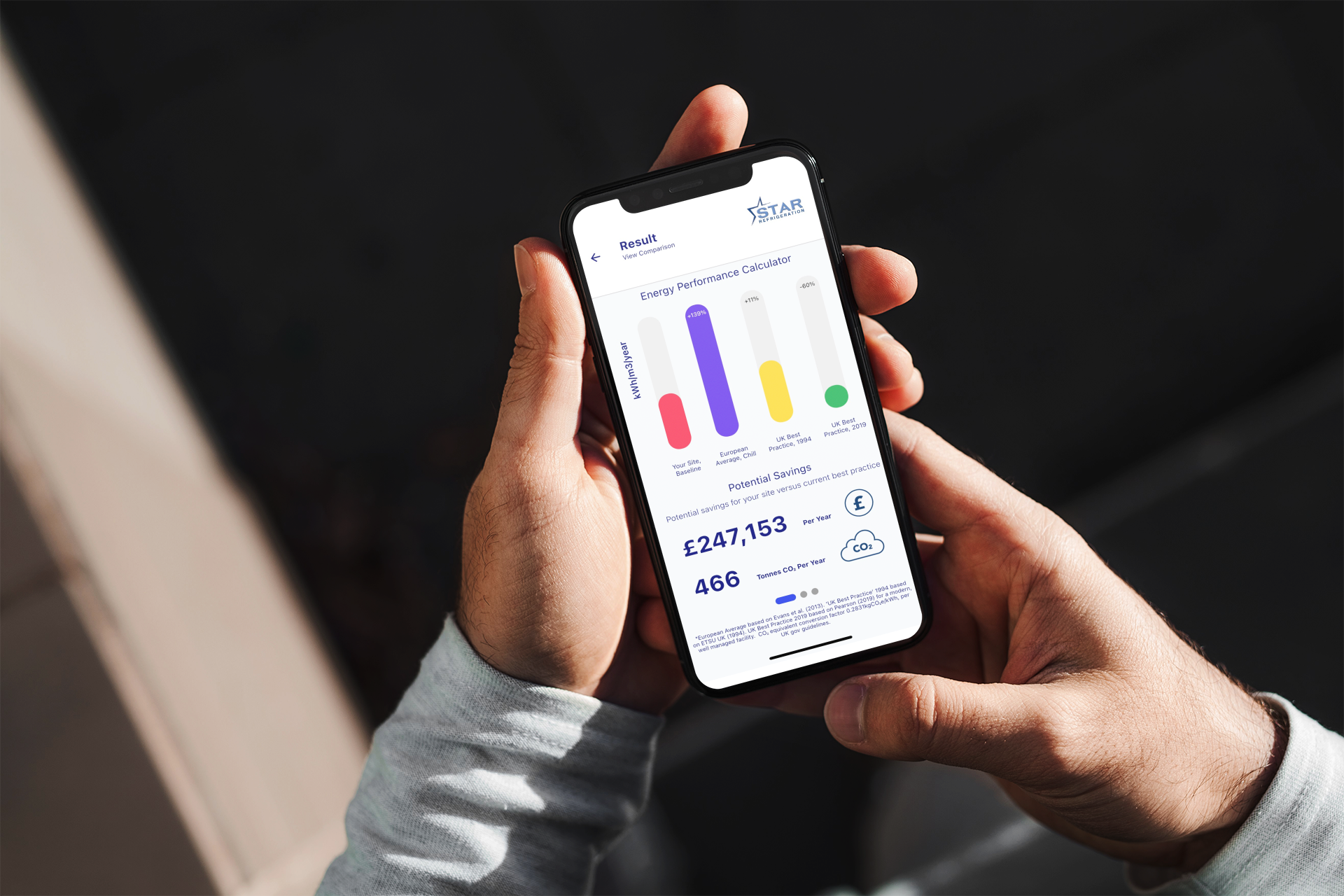
Star Refrigeration free Specific Energy Consumption benchmarking app (SEC Calculator App) launched recently, amidst the build-up to COP26 and much conversation around the need for businesses to meet Climate Change commitments and start on the...Read More
Climate Change and Heat Pumps – ‘We Have The Technology’

There is now a general consensus that climate change is happening and is it’s being dramatically exacerbated by the combustion of fossil fuels. Our heating systems contribute significantly to poor air quality, which presents a...Read More
The essential role of spares in industrial refrigeration plant aftercare

Spares have an essential role in industrial refrigeration plant aftercare. When a component breaks or a fault develops, it is vital that replacement parts are sourced and fitted as soon as possible, to minimise downtime...Read More
Maximise the operational life of your refrigeration plant by investing in comprehensive planned preventative maintenance and asset management services

Refrigeration plant maintenance was once an essentially reactive service, with no engineering input beyond the required safety and compliance checks. Outside these annual service visits, engineers would only attend a customer site to respond to...Read More
A roadmap towards net zero in the cold chain

Transitioning towards a net zero cold chain sector makes sense on multiple levels. Not only will reducing energy consumption and curbing harmful emissions be of benefit to the environment, but it will also incur significant...Read More
Modern Tooling Takes Refrigeration Plant Maintenance to the Next Level

Over the past decade, new technology has made a massive difference to the maintenance service offered to refrigeration end-users by leading refrigeration engineering companies. Technology has enabled refrigeration engineering to move way beyond traditional planned,...Read More
An introduction to modern low carbon refrigeration systems for large distribution centres

The cold chain is responsible for around 2.5% of global greenhouse gas output and finding more efficient and sustainable ways to deliver cooling in response to the UK’s net-zero carbon target is a critical challenge....Read More
Energy Saving Insight: Plant Maintenance & Remote Monitoring Technology

The past two decades have seen a growing commitment across all sectors of UK business and industry to reduce electrical energy consumption to help tackle climate change. In March 2020 the government announced an extension...Read More
Proactive Maintenance to Optimise Efficiency and Reduce Lifecycle Costs

There is no doubt that the initial capital investment made by customers when purchasing and installing refrigeration plant is significant. However, this figure typically only represents around 15% of a refrigeration system’s total lifecycle cost....Read More
The Benefits of Condition Based Maintenance

The Three Levels of Refrigeration Plant Maintenance – Reactive, Proactive and Predictive Operating costs account for around 80% of an industrial refrigeration system’s total lifecycle cost. Over the past 20 years, Star Refrigeration’s Operations Group has...Read More
Maintenance Insight: How Digital Document Management Protects Your Key Business Asset

Good Document Management and Traceability Refrigeration plant is a valuable capital asset and an integral part of many multi-million pound temperature controlled business operations. Star Refrigeration’s Operations team has a proactive approach to plant maintenance...Read More
An Essential Guide to Plant Maintenance

Why Invest in Planned Preventative Maintenance? Refrigeration plant is a key business asset which requires investment in an ongoing programme of planned preventative maintenance (PPM). Traditional PPM features a series of scheduled site visits by...Read More
Carbon Dioxide for Industrial Refrigeration Applications

The resurgence of carbon dioxide The use of carbon dioxide (CO2, R744) as a refrigerant has made a marked resurgence in recent years. In 2008, there were fewer than 150 transcritical installations across the whole...Read More
Cooling and Heating as a Utility…. Reducing Energy Bills and Consumption

Ask most members of the public what utilities they use and most will say gas, electricity and water. Business users are probably in the same boat, and all these utilities will be metered. And this...Read More
Data Collection, Analysis and Reporting in Refrigeration Plant Performance Optimisation

This article describes recent work completed in the area of refrigeration plant performance optimisation, exploring the benefits and limitations of different data collection systems and the challenges of data analysis. The past two decades have...Read More
Minimising Cold & Chill Storage Energy Consumption and Carbon Emissions

Find out how to optimise the efficiency of your temperature-controlled storage unit, thus reducing energy consumption and minimising the costs incurred to your business. An average increase of 30% in energy prices across the last...Read More
F-Gas Conversion

In March 2023, the European Parliament voted for a more aggressive phase-down of hydrofluorocarbon (HFC) gases, aiming for a full phase-out by 2050 and banning HFCs and HFOs in multiple applications from January 2026 and...Read More
New Energy Performance ‘Best Practice’ Guidelines for Cold Store Refrigeration Facilities

How to measure the energy performance of a cold or chill store: using Specific Energy Performance as an efficiency measure enables operators to benchmark energy improvements (kWh/m3/yr) Over the last 25 years, various studies of...Read More
Low Temperature Chillers for Pharma and Petrochemical Industries

Chiller technology has been around for almost 100 years. In that same period, chillers have been used for a myriad of applications in equally numerous configurations and set-ups. It is therefore imperative to consider and...Read More
River Source Heat Pumps for District Heating

How river-based cities across the world could curb greenhouse gas emissions The UK government recently declared a climate emergency, in the wake of environmental protest staged nationally and growing concern for the future of our...Read More
What are the Hidden Costs of an Inefficient Refrigeration System?

A refrigeration system’s efficiency is influenced by a number of factors but one that is often overlooked is refrigerant leakage. It’s estimated that some refrigeration systems have the potential to lose more than 20% of...Read More
How Ethos is Driving Carbon Reduction and Hitting Targets

Ethos helps end users of refrigeration systems save money and cut carbon emissions Time is running out to reverse the effects of global warming, which means the pressure on industry and businesses to reduce their...Read More
Remote Monitoring of Refrigeration and Heating Systems: Challenges and Learning Opportunities

Remote monitoring systems such as Star Technical Solutions specialist software, Ethos, are changing the way companies collect and analyse data from industrial refrigeration and heating plants. Collecting valuable information in real time can help make...Read More
How to Make Sure Your Ammonia Refrigeration Systems are Safe
Ammonia has been for many years the refrigerant of choice for businesses with a need for process cooling, temperature controlled storage and distribution, food and drink manufacturing and many other applications. The benefits of using...Read More
Turning Data into Meaningful Information

In the face of rising energy costs, carbon taxes, and more stringent environmental legislation, regulation and corporate responsibility, businesses operating refrigeration plant face some serious challenges. Metering, monitoring and analysis can help businesses simultaneously ace...Read More
Measurement and Analysis Change Habits to Achieve Improved Efficiency

Rising energy costs, carbon taxes, and achieving the EUs fast approaching 20% carbon reduction target for 2020 regulation leaves responsible businesses with significant challenges. The corporate vision of many businesses is focussed on sustainability and...Read More
Improving the Energy Efficiency of Cooling Systems

Crunching the Numbers The efficiency of a refrigeration system has a direct effect on a business’ environmental and financial performance. This should be in every end-user’s mind when selecting and operating cooling equipment. There are...Read More
Cool in the Face of Challenge – Legislation and Refrigerant Choices

Rob Lamb talks about the considerations plant owners and operators face in terms of refrigerant choices and legislation Given the restrictions placed on F gas production under the European F- gas regulations, the recent response...Read More
F-Gas Regulation and HFC Phasedown

In March 2023, the European Parliament voted for a more aggressive phase-down of hydrofluorocarbon (HFC) gases, aiming for a full phase-out by 2050 and banning HFCs and HFOs in multiple applications from January 2026 and...Read More
Future-Proof Refrigerants: What is the Best Option for Small Industrial Refrigeration Applications?

The Institute of Refrigeration published a paper which describes the refrigerant options available in the future. The phase down of HFCs in Europe under the F-gas regulation and worldwide through the Kigali Amendment to the...Read More
Heat Pumps and Energy Efficiency Influences – Making the right choice

What to look for when purchasing energy efficient heat pumps for district heating & industrial processes. Energy efficient heat pumps are proving to be a clean, affordable and efficient way of heating homes and commercial...Read More
Benefits of Low Charge Ammonia Refrigeration Systems

The low charge ammonia refrigeration insurgency & the HFC phase down Today, the world celebrates the 22nd International Day for the Preservation of the Ozone Layer just days after the world witnessed another major breakthough...Read More
How Planned Preventative Maintenance and Remote Monitoring Can Help Your Businesses Slash Costs and Stay Compliant

In the face of rising energy costs and more stringent environmental legislation and regulation, businesses with operating temperature controlled environments face some serious challenges. Planned aftercare and remote monitoring can help businesses simultaneously ace all...Read More
EcoDesign Directive Minimum Energy Efficiency Standards for Refrigeration Systems – How does the new legislation affect chiller efficiency?

For the last seven years, the European Commission (EC) has been consulting with the industrial refrigeration industry to establish EU-wide rules for minimum energy efficiency and labelling requirements for refrigeration and cooling products. The EcoDesign...Read More
Women in Refrigeration, Air Conditioning and Heat Pump (RACHP) Engineering
Women in Engineering - FemEng Growing equality equals a growing industry Gender inequality is not only a pressing moral and social issue, but also a critical economic challenge. Although there is certain level of fulfilment...Read More
Regular Maintenance and Aftercare – What’s the cost?

Maintenance, Aftercare, Vibration and Condition Site Monitoring of Industrial Refrigeration Systems Refrigeration is vital to the survival, safety and continued operation of businesses. But, more often than not, refrigeration is neglected and relegated to the...Read More
Cutting Costs through Preventative Maintenance and Remote Monitoring

In the face of rising energy costs, soaring carbon taxes, stricter environmental legislation and increasingly stringent regulation, businesses operating temperature controlled environments face some serious challenges. Planned aftercare and remote monitoring can help businesses simultaneously...Read More
F-Gas Regulations – What you Need to Know

In March 2023, the European Parliament voted for a more aggressive phase-down of hydrofluorocarbon (HFC) gases, aiming for a full phase-out by 2050 and banning HFCs and HFOs in multiple applications from January 2026 and...Read More
Winning Solutions to Enhance Cooling System Efficiency

Enhancing The Efficiency of New and Existing Cooling Systems - A Win Win Solution The efficiency of a company’s refrigeration system has a direct effect on environmental and financial performance. This should be in every...Read More